As a mining industry project manager, the success of our projects hinges on the meticulous selection of materials and equipment. One often underestimated yet crucial aspect is the wall thickness of pipes and dredging hoses. This article will delve into the significance of that wall thickness in various industrial projects, particularly in the mining sector.
Not all applications require significant hose wall thickness, but when it’s necessary for the job, it simply cannot be ignored.
Importance of Pipe & Hose Thickness
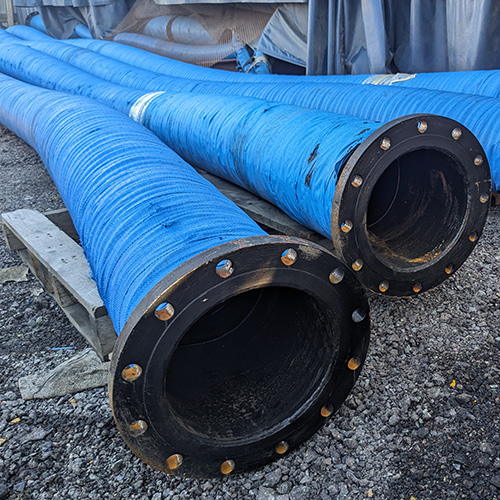
1. Structural Integrity and Pressure Handling
Wall thickness is a paramount consideration when it comes to maintaining the structural integrity of pipes and dredging hoses. In mining operations, these components are subjected to high pressures due to transporting materials such as slurry and water.
Optimal wall thickness is essential to withstand these pressures, ensuring the reliability and safety of the entire system.
2. Abrasion Resistance in Dredging Hoses
Dredging hoses play a pivotal role in mining, facilitating the transport of abrasive materials like sand, gravel, and minerals. A thicker wall in dredging hoses enhances their resistance to abrasion. This is especially critical in mining projects where the conveyed materials can erode less robust hoses, leading to premature failure. Thicker walls contribute to extended hose lifespan and reduced maintenance costs.
3. Impact Resistance in Harsh Environments
Mining environments are notorious for their harsh conditions, including abrasive particles and impacts from heavy materials. Pipes and hoses with adequate wall thickness exhibit superior impact resistance, safeguarding against potential damage. This characteristic is crucial for preventing leaks and ensuring uninterrupted material flow in mining operations.
4. Temperature and Chemical Resistance
In specific mining processes, pipes and hoses are exposed to extreme temperatures and corrosive chemicals. Wall thickness becomes a vital factor in providing insulation against temperature variations and protecting against chemical degradation. Thicker walls contribute to enhanced resistance, ensuring the longevity and efficiency of the piping system in diverse mining applications.
5. Preventing Buckling and Deformation
Thick-walled pipes such as DR11 have inherent strength that prevents buckling and deformation, especially in applications where the pipes may be buried or subjected to external forces. Preventing structural deformities is crucial for maintaining the consistency of material flow and avoiding disruptions in mining operations.
6. Long-Term Cost Considerations
While thicker walls may entail a higher initial investment, such as with DR10 over DR17 they often translate into long-term cost savings. The increased durability and resistance to wear and tear result in reduced maintenance, repair, and replacement costs. Project managers must consider the total cost of ownership, considering the extended service life provided by pipes and hoses with optimal wall thickness.
7. Compliance with Regulatory Standards
Regulatory standards in the mining industry often stipulate minimum requirements for wall thickness to ensure safety and environmental compliance. Adhering to these standards is a legal obligation and a crucial aspect of responsible project management. Thorough consideration of wall thickness contributes to compliance with industry regulations and standards.
In mining industry projects, the importance of pipe and dredging hose wall thickness cannot be overstated. It directly impacts the structural integrity, pressure handling capabilities, abrasion resistance, and overall durability of the entire system. As a mining industry project manager, making informed decisions about wall thickness is essential for ensuring mining operations’ success, safety, and sustainability. Project managers contribute to mining projects’ efficiency, reliability, and long-term viability by prioritizing optimal wall thickness in pipes and hoses.
0 Comments