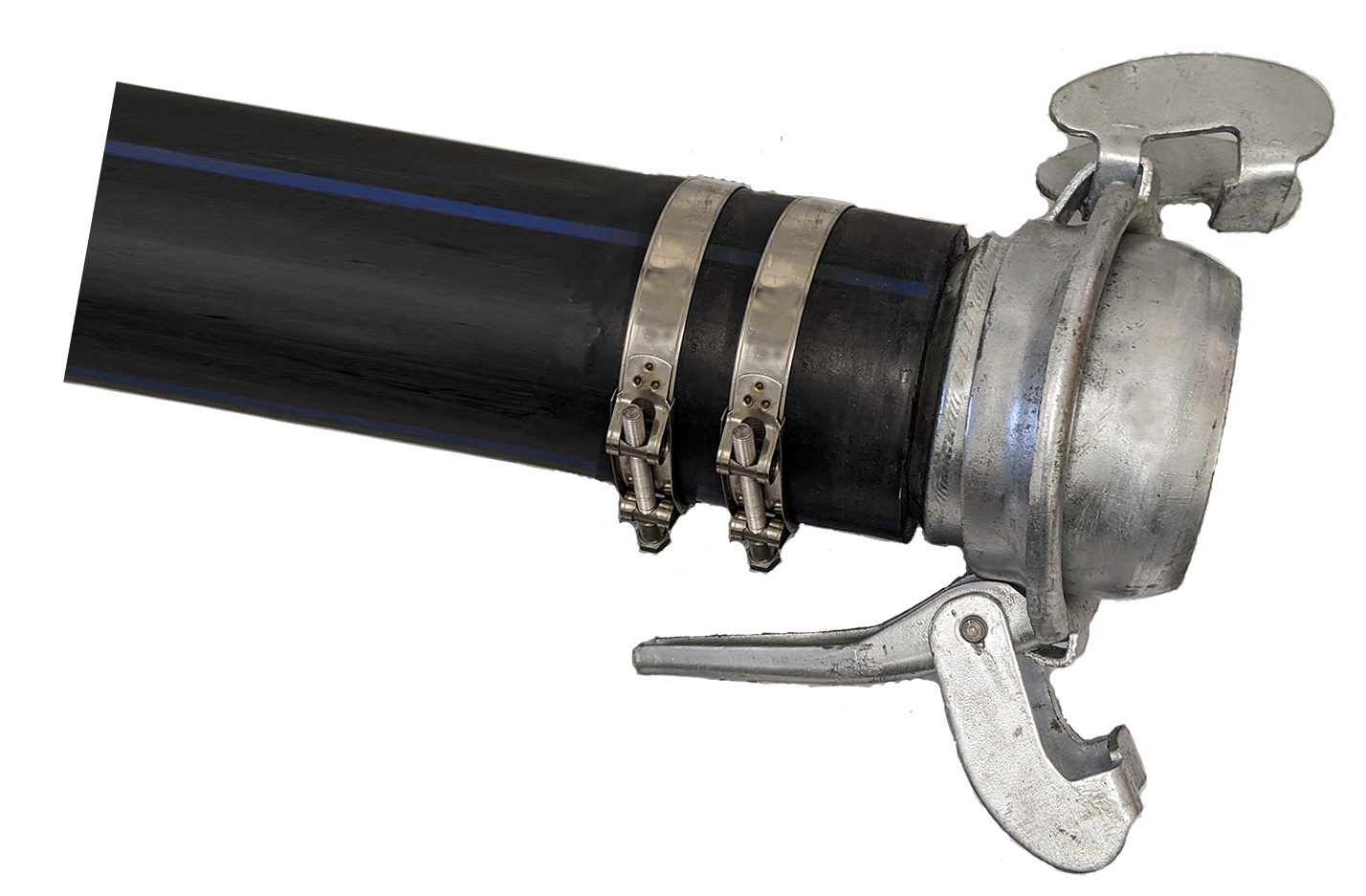
HDPE DR11 Pipe
36-Ft (11m) Sections
HDPE DR11 pipe offers unparalleled advantages in various business and industrial applications. Its high-density polyethylene composition ensures exceptional durability and resistance to corrosion, making it ideal for demanding environments. Plus, with DR11 thickness, this is one of the most robust grades of HDPE pipe on the market.
The standard Bauer fittings ensure quick connections and disconnections, which is critical for short-term or time-sensitive projects.
The HDPE DR11 pipe’s smooth interior surface promotes efficient fluid flow, reducing friction and enhancing overall system performance. And with a lightweight design, HDPE DR11 pipe facilitates easy handling and installation, minimizing labor costs.
DR11 Pipe Specifications
Size | Length | Outer Diameter | Inner Diameter | Thickness | Minimum Quantity | Get Pricing |
---|---|---|---|---|---|---|
3" (75 mm) | 36' (11 m) | 2.95" (75mm) | 2.41" (61.2mm) | 0.268" (6.8mm) | 25 | |
4” (110 mm) | 36' (11 m) | 4.33" (125.0mm) | 3.54" (89.9mm) | 0.394" (10.0mm) | 25 | |
5” (125 mm) | 36' (11 m) | 4.92" (145.0mm) | 4.02" (102.1mm) | 0.449" (11.4mm) | 25 | |
6" (160 mm) | 36' (11 m) | 6.3" (160.0mm) | 5.15" (130.8mm) | 0.575" (14.6mm) | 1 | |
8” (225 mm) | 36' (11 m) | 8.86" (225.0mm) | 7.25" (184.2mm) | 0.807" (20.5mm) | 1 | |
10” (280 mm) | 36' (11 m) | 11.02" (280.0mm) | 9.02" (229.1mm) | 1.000" (25.4mm) | 25 | |
12” (315 mm) | 36' (11 m) | 12.4" (315.0mm) | 10.15" (257.8mm) | 1.126" (28.6mm) | 25 | |
14” (355 mm) | 36' (11 m) | 13.98" (355.0mm) | 11.44" (290.6mm) | 1.268" (32.2mm) | 25 |
Get DR11 Pricing Now!
Talk to our experts about DR11 HDPE pipe for your current or next project.
Call us now or fill out our request form for a prompt estimate.
HDPE DR11 Pipe Rental
Many Anaconda customers use our HDPE DR11 pipe solutions for temporary projects. We offer the flexibility of renting our pipe and hose solutions to ensure that inventory can be returned with relative ease once a project is complete. Please contact us for details.
This pipe is available in 36-foot (11 meters) sections; please let us know your desired length. Quotes will be priced on the entire length of the pipe.
HDPE DR11 pipe comes standard fitted with Bauer Fittings, but may be customized to feature ANSI Flanges, or without any fitting.
Anaconda Pipe & Hose delivers state-of-the-art industrial HDPE DR11 pipe solutions engineered to meet the rigorous demands of diverse applications. Our industrial pipes stand out with the following technical features:
- Bauer Fittings For Easy Connection/Disconnection
Modularity: The use of Bauer fittings provides a quick and easy connection and disconnection of HDPE pipes, allowing for the creation of modular and versatile pipeline systems. This modularity facilitates rapid deployment and adaptation to changing dredging requirements.
- Materials and Construction
Precision Craftsmanship: Anaconda industrial HDPE pipes are crafted from high-quality materials, ensuring durability and longevity in challenging industrial environments.
- Pressure and Temperature Ratings
High-Pressure Capability: Designed to handle varying pressure levels, our pipe ensures reliable fluid conveyance even under high-pressure conditions.
Temperature Resilience: These HDPE pipes are engineered to withstand a broad temperature range, making them suitable for applications in extreme climate conditions.
- Corrosion Resistance
Protective Coatings: Anaconda HDPE DR11 pipe is extremely corrosion-resistant, extending its lifespan and maintaining optimal performance in corrosive environments.
- Dimensional Accuracy
Precision Dimensions: Manufactured with precise measurements to ensure seamless integration with fittings and equipment, minimizing the risk of leaks or inefficiencies.
- Flexibility and Rigidity
Flexibility Options: Depending on the application, Anaconda HDPE pipes offer a range of flexibility, allowing adaptation to various installation configurations.
Structural Integrity: While flexible, these pipes maintain structural integrity to prevent collapse or deformation during operation.
- Quality Assurance
Stringent Testing: Anaconda industrial pipes undergo rigorous quality control and testing procedures, ensuring compliance with industry standards and optimal performance.
Anaconda Pipe & Hose takes pride in delivering industrial HDPE pipes that prioritize durability, performance, and versatility. Our commitment to excellence ensures that Anaconda HDPE DR11 pipe meets the demanding requirements of modern industrial processes, providing reliable solutions for a wide range of applications.
Introduction to Anaconda Pipe And Hose
Anaconda Pipe & Hose stands at the forefront of the HDPE pipe industry, offering high-quality solutions designed to meet the diverse needs of today’s demanding applications. Our HDPE pipe products are engineered for reliability, durability, and exceptional performance, making them the preferred choice for industries ranging from municipal water systems to industrial manufacturing and agricultural irrigation.
We provide customers with convenient access to a comprehensive inventory of HDPE pipe, available in a variety of lengths and configurations. Whether you require straight pipe sold per foot or custom-fitted solutions, our products are priced competitively to ensure value for every purchase. Each HDPE pipe is manufactured using premium materials, resulting in a product that delivers outstanding corrosion resistance and long-term reliability, even in the most challenging environments.
Prior to placing an order, we encourage customers to contact our knowledgeable team to discuss specific requirements, current pricing, and product availability. Our staff is dedicated to helping you navigate the purchasing process, from initial inquiry to final delivery, ensuring a seamless experience. We require a purchase order (PO) for all transactions to maintain accuracy and efficiency, and our terms are designed to ensure a smooth and transparent process for every client.
In addition to our standard HDPE pipe offerings, Anaconda Pipe & Hose provides custom modification services to address unique industry needs. Our experts work closely with customers to design and manufacture tailored solutions, ensuring each product is designed for its intended application. For custom projects, a formal agreement is required prior to commencement, and we are committed to upholding the highest standards throughout the manufacturing process.
We maintain a robust inventory in our store to ensure prompt availability and timely delivery. Customers can view our complete range of HDPE pipe products online or reach out directly with any questions regarding pricing, discounts for bulk orders, or specific application requirements. Our commitment to quality, compliance with industry standards, and dedication to customer satisfaction set us apart as a trusted partner in the HDPE pipe industry.
For more information about our HDPE pipe products, to check current stock, or to discuss your project needs, please contact Anaconda Pipe & Hose. We look forward to providing you with reliable solutions and an exceptional customer experience.
Industrial HDPE DR11 pipe is critical in various industries, offering versatile solutions for fluid transport, material conveyance, and structural applications. Here’s a technical description of the primary industries where industrial HDPE DR11 pipe can find extensive use:
Application: Transmission of crude oil, natural gas, and other hydrocarbons.
Industrial HDPE DR11 pipe in the oil and gas sector withstands high-pressure environments, corrosion-resistant coatings, and stringent material specifications to ensure the safe and efficient transportation of fossil fuels.
2. Chemical Processing Industry
Application: Conveyance of chemicals, acids, and corrosive substances.
Industrial pipes in chemical processing are engineered with materials resistant to chemical corrosion, ensuring their integrity and preventing contamination during fluid transfer.
3. Manufacturing and Processing
Application: Material transport within manufacturing plants and industrial processes.
HDPE DR11 pipe for manufacturing offers precise dimensions, varying flexibility, and compatibility with different materials, facilitating efficient and controlled material flow in diverse production settings.
4. Water and Wastewater Industry
Application: Distribution of clean water and conveyance of wastewater.
Industrial HDPE pipes for water and wastewater feature materials resistant to corrosion and contaminants. They comply with stringent standards to ensure the safe and reliable transport of water in municipal and industrial water systems. The pipe is also critical to various water and geothermal projects, meeting compliance with industry standards.
Application: Structural support, water supply, and material transport on construction sites.
Industrial pipes offer key structural integrity and durability benefits in construction. They may be used for scaffolding, underground utilities, or conduits for various construction materials.
Application: Transport of ores, minerals, and slurry in mining operations.
Industrial pipes in mining are designed to handle abrasive materials, high pressures, and challenging terrain. Their abrasion-resistant coatings and robust construction ensure longevity in demanding mining environments.
Application: Transport of fluids in power plants, including steam and cooling water.
Industrial HDPE pipes in power generation can endure high temperatures and pressures. They are often designed with materials suitable for steam transport and offer corrosion-resistant coatings for longevity.
Application: Conveyance of water for irrigation, fertilizers, and pesticides.
Agricultural industrial pipes must be flexible, durable, and resistant to UV exposure. They are utilized in irrigation systems, ensuring efficient water distribution in agricultural fields.
9. Food and Beverage Industry
Application: Transport of liquids in food and beverage processing plants.
Industrial HDPE pipes in the food industry are made from materials compliant with food-grade standards. They prevent contamination and maintain the hygienic standards required in food processing.
10. Automotive and Aerospace Manufacturing
Application: In automotive and aerospace manufacturing, industrial pipes require precision and resistance to hydraulic fluids and coolants. They play a crucial role in maintaining the efficiency of manufacturing systems.
Industrial HDPE DR11 pipe is indispensable in numerous industries, each demanding specific technical characteristics to meet the challenges of their respective applications. Whether conveying fluids, supporting structures, or facilitating manufacturing processes, HDPE DR11 pipe contributes significantly to the seamless and efficient operation of diverse industrial sectors.
Bauer Fittings
Bauer fittings stand out as versatile and reliable components in any kind of industrial pipe system, offering a range of technical advantages that contribute to efficient fluid handling and ease of use. These fittings, also known as “Bauer Couplings”, are well established because of their quick and secure connection capabilities, providing numerous benefits for various industries. Here’s a detailed look at the technical advantages of Bauer fittings (also known as Bauer Couplers) particularly when it comes to HDPE pipe:
1. Rapid and Secure Connection
Bauer fittings are designed for quick and efficient coupling. Their innovative design allows for rapid connection and disconnection, significantly reducing downtime during pipe assembly or disassembly. The secure connection ensures leak-free operations, promoting overall system reliability and environmental safety.
2. Versatile Applications
Bauer fittings find application across diverse industries, including agriculture, construction, dredging, mining, and more. Their versatility stems from the ability to connect pipes of various materials and sizes, providing a standardized and adaptable solution for different fluid transport needs.
3. Durable and Robust Construction
Bauer fittings are constructed from robust materials, often high-quality galvanized steel, ensuring durability and resistance to corrosion. This robust construction allows the fittings to withstand the rigors of even the most difficult industrial environments, providing a long service life and minimizing the need for frequent replacements.
4. Sealing Mechanism
Bauer fittings incorporate a reliable sealing mechanism for HDPE pipe, ensuring a tight, leak-proof connection. EPDM or NBR gaskets enhance the sealing properties, making the fittings suitable for a wide range of fluids, including water, chemicals, and slurry.
5. Pressure Ratings
Bauer fittings are engineered to handle varying pressure requirements. The fittings are available in different pressure classes, allowing users to select the appropriate fittings based on the specific demands of their applications. This flexibility ensures compatibility with a broad range of industrial systems.
6. Ease of Handling and Operation
The design of Bauer fittings incorporates user-friendly features, making them easy to handle and operate. The quick-locking mechanism simplifies the connection process, enabling operators to manage pipe systems with minimal effort efficiently.
7. Interchangeability
One notable technical advantage of Bauer fittings is their interchangeability. Fittings of the same size and type from different manufacturers can often be used interchangeably, and even with different pipe materials. This interchangeability enhances flexibility in sourcing components and simplifies maintenance and repairs because there is no need for additional pipe fusing or welding.
8. Reduced Maintenance Requirements
The durability and robustness of Bauer fittings contribute to reduced maintenance needs. Their resistance to corrosion and wear minimizes the risk of component failure, resulting in lower maintenance costs and increased operational efficiency.
9. Cost-Effective Solutions
Bauer fittings offer easily the most cost-effective HDPE DR11 pipe connection solutions for fluid handling applications. The ease of installation, interchangeability, and durability massively contribute to overall labor cost savings, making them an economical choice for companies seeking reliable and efficient pipe connections.
10. Safety & User Friendly
Bauer fittings are designed with user safety in mind. The assembly process is straightforward, reducing the risk of accidents or injuries during pipeline connections and disconnections.
11. Wide Range of Accessories
Bauer fittings come with various complementary accessories, such as caps, plugs, and reducers. These accessories enhance the versatility of the fittings, allowing users to customize and optimize their pipe systems according to their own specific requirements.
Bauer fittings provide a robust and versatile solution for industrial pipe systems. Their technical benefits, including rapid connection, durability, and versatility, make them a preferred choice for industries where efficient fluid handling is paramount.
ANSI Flange Fittings
ANSI flange fittings are integral components in Anaconda HDPE DR11 pipe systems, renowned for their standardized design and versatile applications. These fittings adhere to the American National Standards Institute (ANSI) specifications, providing a range of technical advantages for fluid handling in various industries. Here’s a detailed examination of the technical benefits of ANSI flange fittings:
1. Standardized Design
ANSI flange fittings follow standardized dimensions and specifications, ensuring uniformity across manufacturers. This standardization allows for the interchangeability of ANSI flanges and fittings, simplifying procurement and maintenance processes.
2. Ease of Installation
The design of ANSI flange fittings facilitates easy installation and removal. The bolt-hole patterns and flange faces adhere to ANSI standards, enabling quick alignment and connection. This ease of installation reduces labor costs and downtime during pipe assembly or modifications.
3. Wide Range of Applications
ANSI flange fittings find application in diverse industries, including oil and gas, fisheries, chemical processing, and more. Their standardized design allows for compatibility with various pipe and hose materials and fluids, making them suitable for a wide variety of applications.
4. Durable and Corrosion-Resistant Construction
ANSI flange fittings are commonly constructed from carbon steel, stainless steel, or alloy steel, ensuring durability and corrosion resistance. This robust construction enhances the longevity of the fittings, making them suitable for harsh industrial environments.
5. Pressure and Temperature Ratings
ANSI flange fittings are engineered to meet specific pressure and temperature ratings, allowing for safe and reliable performance in various operating conditions. These fittings are available in different classes, providing flexibility for users to select fittings based on their specific system requirements.
6. Sealing Mechanism
ANSI flange fittings incorporate a gasket sealing mechanism. Using materials like compressed rubber, or PTFE ensures a reliable and leak-free seal between mating flanges. The sealing mechanism contributes to the integrity of the pipe system, preventing fluid leaks.
7. Versatility in Flange Types
ANSI standards encompass various flange types, such as slip-on, weld neck, blind, and lap joint flanges. This versatility allows users to choose the appropriate flange type based on their specific application and system requirements, enhancing flexibility in design.
8. Facilitates Piping System Maintenance
The standardized design of ANSI flange fittings simplifies maintenance and repairs. The ease of disassembly and reassembly with ANSI flanges enables quick access to components, reducing downtime during maintenance activities and minimizing disruption to industrial processes.
9. Compliance with Industry Standards
ANSI flange fittings adhere to industry standards, ensuring compliance with safety and quality requirements.
10. Facilitates System Expansion
The standardized nature of ANSI flange fittings allows for straightforward system expansion or modification. Anaconda pipes with ANSI fittings do tend to include a rotatable ANSI flange on one end of the hose or pipe, adding to overall installation ease. Additional components can be easily integrated into existing piping systems, contributing to the adaptability and scalability of industrial installations.
Opting for Straight Lengths Without Fittings
While standard industrial practice involves incorporating fittings into pipe and hose applications for various purposes, there may be specific scenarios where opting for straight lengths without fittings can have certain benefits. It’s essential to understand the technical considerations and potential advantages of such a choice:
1. Reduced Friction and Flow Resistance
Straight HDPE DR11 pipe lengths, without including fittings, can offer a smoother and more streamlined fluid flow path. The absence of abrupt changes in direction minimizes frictional resistance and turbulence, potentially enhancing overall flow efficiency. HDPE DR11 pipe is available in various lengths, and selecting the appropriate length is important when ordering for specific applications.
2. Simplified Maintenance
Straight lengths of pipe can, in some instances, simplify maintenance procedures. Without fittings, fewer components are prone to wear or potential failure points. This could reduce the frequency and complexity of maintenance activities, contributing to a more straightforward and cost-effective maintenance regime on a very long term basis.
3. Custom Length Configurations
Opting for straight lengths allows for custom configurations tailored to specific project requirements. While standard HDPE DR11 pipe lengths are common, the ability to customize lengths without additional fittings can be advantageous for achieving precise dimensions in a piping system. Please note that additional fees may be charged for custom lengths or special shipping requirements.
4. Minimized Risk of Leakage
Fittings are potential points of vulnerability for leaks. Minimizing the number of fittings can reduce the overall risk of leakage in the system. This is particularly relevant in applications where leak prevention is critical, such as in systems handling hazardous materials.
5. Streamlined Installation
The absence of fittings simplifies the installation process. Straight lengths can be easier to handle and align during installation, potentially reducing labor costs and installation time. This streamlined process could be advantageous in large-scale projects with extensive piping networks.
6. Enhanced Structural Integrity
Straight lengths contribute to a more continuous and uniform structure. This can enhance the overall structural integrity of the piping system, particularly in applications where stability and resistance to external forces are crucial considerations.
7. Optimized Flow Dynamics
A piping system composed of straight lengths can offer optimized flow dynamics. The absence of fittings-related disruptions allows for a more predictable and controlled flow pattern, which can be important in applications requiring precise fluid dynamics.
8. Cost Savings in Some Cases
Depending on the project requirements, material costs, and installation considerations, opting for straight lengths without fittings may result in cost savings. The price of HDPE DR11 pipe may vary per foot, with discounts available for bulk orders.
9. Specialized Applications
In specific specialized applications where fittings are not required due to the nature of the fluid, pressure requirements, or system design, using straight lengths without fittings can be a technically viable option.
10. Adherence to Project Specifications
This configuration ensures design requirements and specifications compliance in scenarios where project specifications explicitly call for straight lengths without fittings.
It’s crucial to note that the decision to use HDPE DR11 pipe lengths without fittings should be made based on a thorough understanding of the specific project requirements, industry standards, and regulatory considerations. While there can be potential benefits, the choice must align with the technical and safety requirements of the industrial application. In our experience, HDPE DR11 pipe with no fittings can create connection and disconnection difficulties and delays that are eliminated by Bauer or ANSI fittings. Consulting with engineers and adhering to industry best practices is essential in making informed decisions regarding piping configurations.
For more details, we invite you to begin viewing the available HDPE DR11 pipe lengths and pricing information on our product listing or online catalog page.