Anaconda industrial hoses and pipes for fluid transport are crucial in oil, gas, and power operations.
Home
Industries
Energy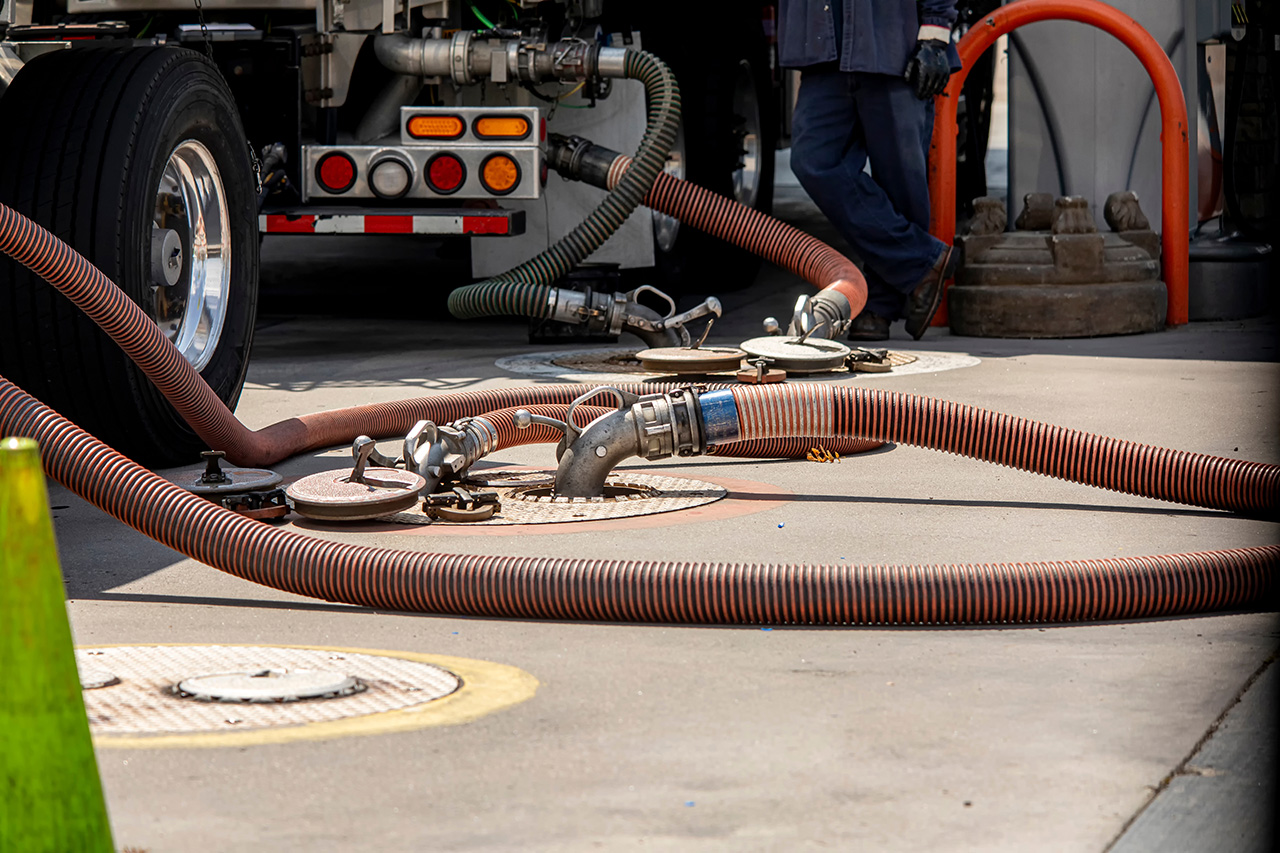
Table Of Contents
HDPE Pipe | Discharge Hose | Lay Flat Hose | Hose Floats
How HDPE Pipe Is Used In Energy Projects
Anaconda Pipe and Hoses play a crucial role in the oil and gas industry, where they are essential components for transporting, controlling, and directing fluids within various processes. Here are some key ways these are used in the oil and gas industry:
- Pipeline Construction: Used to connect and join sections of pipelines, ensuring a secure and leak-free flow of crude oil, natural gas, and other fluids from extraction sites to processing facilities and distribution points.
- Wellheads and Downhole Equipment: Utilized in wellheads and downhole equipment, connecting casing and tubing to control the flow of oil or gas from the reservoir to the surface.
- Oil and Gas Processing Plants: Employed in processing plants to connect equipment such as pumps, compressors, separators, and heat exchangers, facilitating the efficient processing and separation of hydrocarbons.
- Refineries: Transferring crude oil and refined products between various units, such as distillation towers, catalytic converters, and storage tanks.
- Distribution and Storage: Used in storage tanks and terminals to connect pipes for loading, unloading, and transferring oil and gas products to distribution networks, such as pipelines, trucks, and railcars.
- Hydraulic Systems: Crucial components in hydraulic systems, which control valves, actuators, and other equipment used in oil and gas production and processing.
- Instrumentation and Control: Utilized to install instrumentation devices, such as pressure gauges, temperature sensors, and flow meters, to monitor and control the flow and pressure of fluids.
- Emergency Shutdown Systems: Part of emergency shutdown systems that enable quick isolation and shutdown of equipment during emergencies or maintenance.
- Offshore Platforms: Used on offshore platforms to connect pipelines for transporting oil and gas from underwater wells to the platform and onshore facilities.
- Gas Compression and Injection: Play a role in gas compression and injection systems, where they help in compressing and injecting natural gas into reservoirs to enhance oil recovery.
In the Oil and Gas industry, Anaconda Pipe and Hoses contribute to the safe, efficient, and reliable operation of exploration, production, processing, and distribution activities. They are designed to withstand high pressures, corrosive environments, and challenging conditions in this industry.
Benefits Of HDPE Pipe For Energy (Oil & Gas)
Industrial HDPE pipe plays a pivotal role in the energy sector, offering a range of technical benefits that contribute to the efficiency, safety, and reliability of operations. Here are the key advantages of HDPE pipe in the oil and gas industries:
- High-Pressure Resistance
HDPE pipes in the oil and gas sector are engineered to withstand high-pressure conditions. The materials used and the design ensure the pipes can safely transport fluids, including crude oil and natural gas, under the intense pressures of extraction and transmission processes.
- Corrosion Resistance
Corrosion is a significant concern in the oil and gas industry due to the presence of corrosive substances. Industrial pipes are equipped with corrosion-resistant coatings, often made of specialized alloys, to extend their lifespan and maintain their structural integrity in harsh environments.
- Temperature Tolerance
Oil and gas extraction and transmission involve varying temperatures, from extreme cold to high heat. Industrial pipes are designed to withstand a wide temperature range, ensuring they remain functional and durable in diverse climatic conditions.
- Material Compatibility
Industrial pipes used in the oil and gas industry are compatible with various hydrocarbons and fluids encountered in extraction and transportation. The material selection is crucial to prevent chemical reactions, maintain fluid purity, and ensure the pipes’ longevity.
- Precision Dimensions
Accurate dimensions are vital for seamless integration with various components, such as valves and fittings. Industrial pipes maintain precision in their dimensions, ensuring secure connections and minimizing the risk of leaks or inefficiencies in the system.
- Flexibility and Durability
Flexibility is crucial for accommodating various installation configurations and handling dynamic conditions in the oil and gas sector. While offering flexibility, industrial pipes maintain structural durability to prevent collapse or deformation during operation.
- Resistance to Abrasion
In pipelines transporting crude oil and natural gas, abrasion from particulate matter is a concern. Industrial pipes are often equipped with abrasion-resistant features, including coatings or materials, to withstand the erosive effects of transported fluids.
- Compatibility with Industry Standards
Adherence to industry standards is paramount for safety and regulatory compliance. Industrial pipes are manufactured to meet or exceed standards set by organizations such as the American Petroleum Institute (API) to ensure the highest level of quality and performance.
- Weldability and Joining Methods
Weldability is a critical aspect of industrial pipes for the oil and gas industry. Pipes are designed for efficient welding processes, and various joining methods, including butt welding and threading, are employed to create secure and leak-resistant connections.
- Customization for Specific Applications
The oil and gas industry encompasses diverse applications, each with unique requirements. Industrial pipes can be customized in terms of material composition, diameter, and length to suit the specific demands of various extraction, transmission, and refining processes.
In summary, Anaconda’s industrial HDPE pipes in the oil and gas industries offer a combination of technical features that ensure reliability, durability, and safety. Their ability to withstand extreme conditions, resist corrosion, and maintain precise dimensions makes them indispensable components for oil and gas facilities’ successful and efficient operation.
Anaconda Suction & Discharge Hoses for Energy
Discharge hoses are critical components in the oil and gas industry, offering key technical advantages essential for fluid transfer, oil suction, and versatile applications. Here’s a technical description of the primary benefits of suction hoses in the oil and gas sector:
- Fluid Transfer
Benefit: Efficient Handling of Oil and Petroleum Products
Suction hoses are designed for the transfer of oil, fuel, and petroleum-based products within oil and gas facilities.
Technical Advantage: Constructed with materials compatible with hydrocarbons, the hoses ensure reliable and efficient fluid transfer, meeting industry standards.
- Oil Suction
Benefit: Effective Suction of Oil from Wells and Tanks
Suction hoses are crucial for extracting oil from wells, tanks, or drilling operations in the oil and gas exploration and production phases.
Technical Advantage: The hoses are engineered with reinforced construction and vacuum resistance to maintain structural integrity during high-suction operations.
- Chemical Resistance
Benefit: Compatibility with Harsh Chemicals in Oil and Gas Processes
Suction hoses can be manufactured with materials resistant to chemicals commonly encountered in oil and gas operations.
Technical Advantage: Chemical resistance ensures that the hoses maintain structural integrity when exposed to corrosive substances, contributing to a longer service life.
- Flexibility and Maneuverability
Benefit: Adaptability to Dynamic Oil and Gas Environments
Oil and gas facilities often involve dynamic equipment configurations and changing operational conditions. Suction hoses are designed with flexibility to navigate these environments.
Technical Advantage: The hoses’ flexibility ensures efficient and adaptable material transfer, suction, and discharge in diverse oil and gas scenarios.
- Resistance to Abrasion
Benefit: Extended Service Life in Harsh Oil and Gas Environments
Oil and gas environments can be abrasive due to the presence of particles and debris. Suction hoses are constructed with materials offering high abrasion resistance.
Technical Advantage: This resistance ensures durability, reducing the need for frequent hose replacements and minimizing downtime in oil and gas operations.
- Custom Sizing for Flow Optimization
Benefit: Tailored Solutions for Varied Oil and Gas Applications
Industrial suction hoses are available in various sizes and diameters, allowing for customization based on the specific flow requirements of different oil and gas processes.
Technical Advantage: Proper sizing ensures optimal flow rates, minimizing energy consumption and pressure drops, and maximizing the efficiency of material transfer in oil and gas operations.
- Vacuum Resistance
Benefit: Optimized Suction Performance in Demanding Conditions
Suction hoses are engineered to withstand varying degrees of vacuum, ensuring effective suction of liquids and materials in different oil and gas applications.
Technical Advantage: The hoses’ vacuum resistance maintains structural integrity, optimizing suction performance and preventing collapse during demanding oil and gas processes.
In summary, suction hoses in the oil and gas industry offer technical advantages, including efficient handling of oil and petroleum products, effective oil suction, chemical resistance, flexibility, resistance to abrasion, custom sizing, and vacuum resistance. These features collectively contribute to the durability, adaptability, and overall effectiveness of suction hoses in meeting the unique challenges of oil and gas applications.
Anaconda Lay Flat Hose for Energy
Industrial lay flat hoses play a crucial role in the oil and gas industry, providing technical advantages that optimize fluid transfer processes and enhance operational efficiency. The key benefits of industrial lay flat hoses in the oil and gas sector include:
- Chemical Resistance
Benefit: Compatibility with Oil and Gas Fluids
Industrial lay-flat hoses are engineered with materials that resist chemicals commonly found in oil and gas operations. This ensures compatibility with various fluids encountered in the industry, enhancing the hoses’ longevity and performance.
- High Burst Pressure Capability
Benefit: Reliability Under High-Pressure Conditions
These hoses are engineered to withstand high burst pressures and maintain structural integrity and reliability in oil and gas applications. The high burst pressure capability ensures dependable fluid transfer even under elevated pressures.
- Resistance to Abrasion and Impact
Benefit: Durability in Rigorous Oil and Gas Environments
Constructed with robust materials, lay flat hoses resist abrasion and impact, crucial in the rugged conditions of oil and gas operations. This durability minimizes the risk of hose damage during handling and fluid transfer.
- Oil and UV Resistance
Benefit: Longevity in Outdoor Exposure
Lay flat hoses resist oil and UV radiation, common elements in outdoor oil and gas operations. This resistance ensures prolonged service life and performance, even when exposed to sunlight and petroleum-based substances.
- Quick Deployment and Retrieval
Benefit: Time-Efficient Operations
The flat design allows for rapid deployment and retrieval, facilitating time-efficient operations on oil and gas sites. Quick hose handling contributes to overall productivity and operational efficiency.
- Flexibility and Maneuverability
Benefit: Adaptability to Dynamic Oil and Gas Configurations
Lay flat hoses exhibit flexibility, enabling them to adapt to changing oil and gas site configurations and contours. This flexibility ensures efficient material transfer and fluid handling in dynamic and challenging environments.
- Uniform Fluid Distribution
Benefit: Consistent Transfer of Oil and Gas Fluids
Lay flat hoses distribute fluids uniformly along their length, ensuring consistent transfer and distribution of oil, gas, or other petroleum-based liquids. This is critical for maintaining operational efficiency and optimizing fluid usage.
- Compatibility with Oil and Gas Equipment
Benefit: Seamless Integration with Industry Machinery
Designed for compatibility with oil and gas pumps and equipment, these hoses feature fittings and couplings that provide a secure connection. This minimizes the risk of leaks and ensures efficient fluid transfer within the oil and gas operation.
- Custom Sizing for Flow Optimization
Benefit: Tailored Solutions for Varied Oil and Gas Flow Rates
Lay flat hoses are available in various sizes and diameters, allowing for customization based on the specific flow requirements of different oil and gas applications. This ensures optimal fluid transfer rates and minimizes energy consumption.
- Temperature Resistance
Benefit: Suitability for Varied Oil and Gas Climates
Engineered to withstand a broad temperature range, these hoses remain functional in diverse oil and gas climates. Their flexibility and reliability are maintained even in extreme temperature conditions encountered in the industry.
In summary, industrial lay flat hoses offer technical benefits that contribute to the efficiency, durability, and adaptability of fluid transfer processes in the oil and gas industry. Their chemical resistance, high burst pressure capability, and compatibility with industry machinery make them essential for optimizing oil and gas operations.
Industrial Hose Floats for Energy
Industrial hose floats play a critical role in offshore oil and gas operations, providing essential advantages that enhance the efficiency, safety, and reliability of hoses used for fluid transfer between platforms and vessels. Here’s a technical description of the key benefits of industrial hose floats in the context of offshore oil and gas:
- Buoyancy Enhancement
Industrial hose floats are engineered to significantly enhance buoyancy, ensuring that hoses remain afloat on the water surface during offshore oil and gas operations. This buoyancy is crucial for maintaining the integrity of fluid transfer systems and preventing submersion of hoses.
- Stability and Position Control
The buoyant design of industrial hose floats contributes to stability and precise control of hose positions. This is critical in offshore environments where controlled fluid transfer is essential. Stable hoses prevent sagging or tilting, ensuring uniform fluid distribution and efficient transfer between platforms and vessels.
- Abrasion Resistance
Offshore oil and gas operations involve the transport of fluids containing abrasive elements. Industrial hose floats are constructed with materials that offer high abrasion resistance, protecting the hoses from wear and tear caused by the abrasive nature of the fluids being conveyed.
- Corrosion Resistance
Offshore environments expose hoses to corrosive elements such as seawater. Industrial hose floats are engineered with corrosion-resistant materials to withstand exposure to saltwater and other corrosive elements, ensuring the floats maintain their structural integrity in challenging offshore conditions.
- UV Resistance
Offshore operations often entail prolonged exposure to sunlight. Industrial hose floats are designed with UV-resistant materials and coatings to withstand UV radiation, ensuring the longevity of the floats and maintaining their structural integrity in challenging environmental conditions.
- Impact Resistance
In dynamic offshore environments, hoses may be exposed to impacts and collisions during fluid transfer activities. Industrial hose floats are designed to withstand such impacts, contributing to the overall durability of the floats and ensuring their effectiveness in offshore operations.
- Modular Design for Flexibility
Some industrial hose floats used offshore feature a modular design. This allows them to be connected or stacked, providing flexibility in adapting to different hose lengths and configurations. The modular design enhances the versatility of the floats, catering to the varying requirements of offshore fluid transfer applications.
- Attachment Mechanisms
To ensure secure and stable positioning, industrial hose floats incorporate efficient attachment mechanisms. These mechanisms, such as clamps or straps, are designed to securely fasten the floats to the hoses, preventing displacement and maintaining the desired alignment during offshore fluid transfer operations.
- Ease of Installation and Maintenance
Industrial hose floats are engineered for ease of installation and maintenance. The design allows for straightforward attachment to hoses, and the floats are easily inspected for wear or damage. This ease of maintenance contributes to the overall reliability and longevity of the equipment used in offshore oil and gas operations.
- Compliance with Industry Standards
Quality industrial hose floats used offshore adhere to relevant industry standards and regulations. Compliance ensures that the floats meet the necessary safety and performance criteria, providing operators with confidence in the reliability and effectiveness of the equipment during offshore fluid transfer activities.
In summary, industrial hose floats offer significant technical benefits in offshore oil and gas operations by enhancing buoyancy, stability, and durability of hoses used for fluid transfer. Their engineered features contribute to fluid transfer systems’ overall efficiency and safety, making them essential components in the challenging and dynamic offshore environment.