Anaconda industrial hoses and pipes offer effective conveyance in logging, timber processing, and aquaculture operations.
Home
Industries
Manufacturing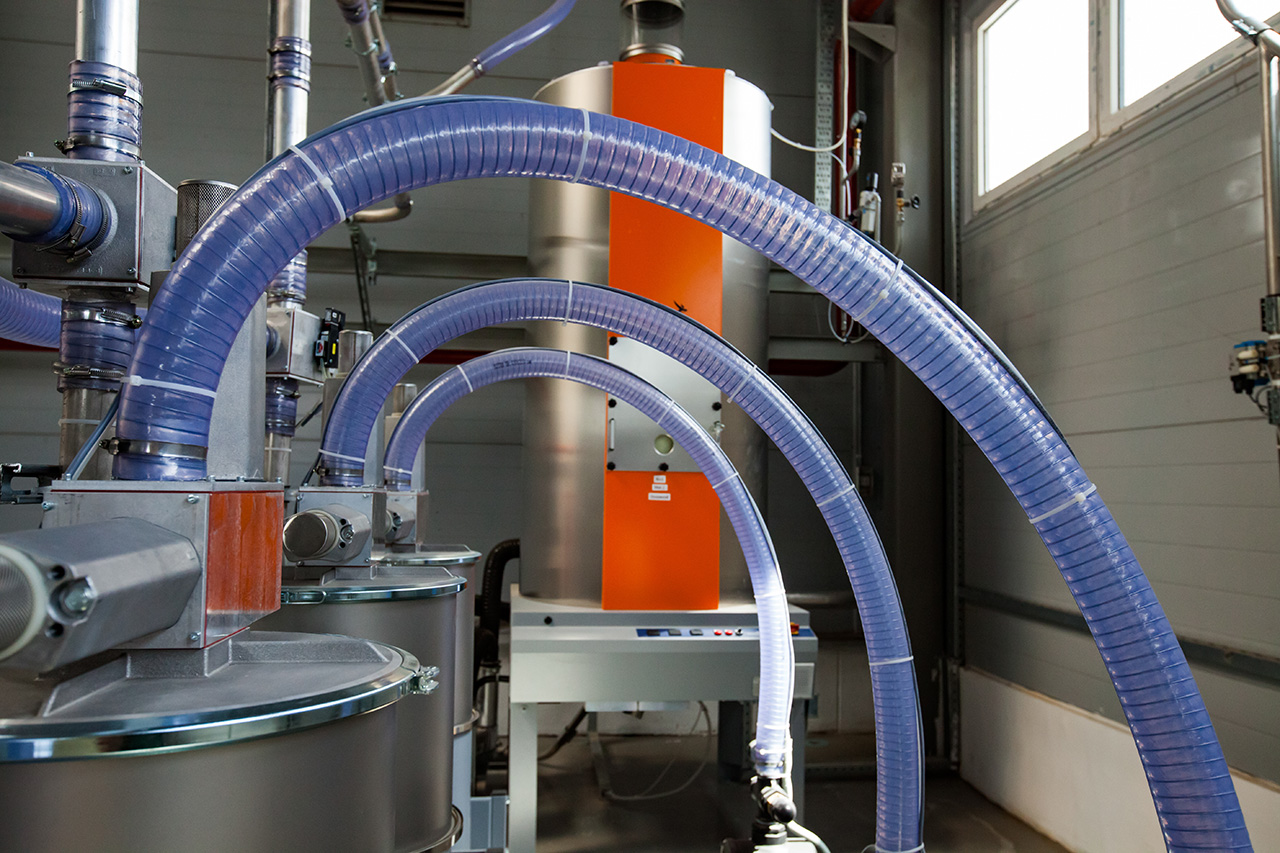
Industrial Pipe & Hose For Manufacturing
Table Of Contents
HDPE Pipe for Manufacturing | Industrial Pipe for Automotive/Aerospace Manufacturing | Discharge/Suction Hose for Manufacturing | Lay Flat Hose for Manufacturing
HDPE Pipe for Manufacturing
Industrial HDPE pipe plays a crucial role in manufacturing and processing operations, providing various technical benefits that contribute to efficiency, reliability, and seamless material flow. The key advantages of industrial HDPE pipe in the manufacturing and processing industries include:
1. Efficient Fluid Transfer
Industrial HDPE pipe facilitates the efficient transfer of fluids, ensuring a streamlined manufacturing process. Their smooth interior minimizes friction loss, optimizing the flow of liquids within the manufacturing and processing systems.
2. Pressure Handling
Designed to handle varying pressure levels, heavy duty polyethylene pipe offer reliable performance under different manufacturing conditions. They are engineered to withstand high pressures, providing stability and safety in fluid conveyance.
3. Corrosion Resistance
Industrial HDPE pipes are constructed with materials that resist corrosion, ensuring durability and longevity in manufacturing environments. Corrosion-resistant coatings protect against chemical reactions, maintaining the integrity of the pipes.
4. Precision Dimensions
Accurate dimensions are crucial for seamless integration with manufacturing equipment. Industrial pipes maintain precise measurements, allowing for secure connections and minimizing the risk of leaks or inefficiencies in production.
5. Flexibility and Durability
Industrial HDPE pipes offer a balance of flexibility and durability. This flexibility allows them to adapt to different manufacturing configurations while their robust construction ensures structural integrity, preventing deformation or collapse.
6. Temperature Tolerance
Manufacturing processes often involve fluctuating temperatures. Industrial HDPE pipes are engineered to withstand a broad temperature range, ensuring they remain functional and durable in diverse manufacturing climates.
7. Material Compatibility
Industrial pipes are compatible with a variety of materials used in manufacturing, including liquids, gasses, and granular substances. The material selection is tailored to the specific requirements of different manufacturing applications.
8. Customization for Specific Applications
Manufacturing processes vary widely. Industrial pipes can be customized in terms of material composition, diameter, and length to suit the specific flow requirements and material characteristics of different manufacturing applications.
9. Joining Methods
Efficient joining methods, such as welding, threading, or specialized connectors, are crucial in manufacturing. Industrial pipes are designed for secure and leak-resistant connections, minimizing the risk of fluid leaks during production.
10. Abrasion Resistance
In manufacturing processes involving abrasive materials, industrial pipes can be equipped with abrasion-resistant features. This ensures longevity and optimal performance in the presence of abrasive substances.
11. Safety Compliance
Adherence to safety standards is paramount in manufacturing. Industrial pipes are manufactured to meet or exceed industry safety standards and regulations, providing a secure and reliable infrastructure for material transport.
12. Easy Maintenance and Inspection
Industrial pipes are designed for easy maintenance and inspection. Accessible areas for inspection and maintenance facilitate regular checks, ensuring the ongoing reliability and safety of the manufacturing systems.
In summary, industrial pipes are essential components in the manufacturing and processing industries, offering technical features that contribute to the efficiency, reliability, and safety of material transport within diverse production settings. Their precision dimensions, material compatibility, and resistance to corrosion make them integral to the seamless operation of manufacturing processes.
Anaconda Industrial Pipes for Automotive & Aerospace Manufacturing
Industrial pipes are vital components in the automotive and aerospace manufacturing industries, providing technical advantages that contribute to efficient fluid transport, precision machining, and overall system reliability. Here’s a detailed technical description of the key benefits of industrial pipes in these sectors:
1. Precision Fluid Transport
Industrial pipes enable precise fluid transport in automotive and aerospace manufacturing processes. Their accurate dimensions and smooth interiors minimize friction loss, ensuring the efficient flow of coolants, lubricants, and hydraulic fluids critical for machining and assembly.
2. High-Pressure Handling
Automotive and aerospace manufacturing often involve high-pressure hydraulic systems. Industrial pipes are engineered to handle elevated pressures, ensuring the safe and reliable conveyance of fluids required for hydraulic applications in machining and assembly.
3. Corrosion Resistance
Industrial pipes used in these industries are designed with corrosion-resistant materials and coatings. This is crucial for withstanding exposure to cutting fluids, coolants, and hydraulic oils, which may contain corrosive elements that can degrade conventional materials.
4. Temperature Control
Precision manufacturing processes in automotive and aerospace industries require precise temperature control. Industrial pipes are engineered to handle temperature fluctuations, ensuring the maintenance of optimal temperatures during fluid transport and machining operations.
5. Material Compatibility
Industrial pipes are compatible with a variety of fluids used in machining and manufacturing, including cutting oils, coolants, and hydraulic fluids. The material selection prevents contamination and ensures the integrity of transported substances.
6. Precision Dimensions for Machining
Accurate dimensions are crucial for machining operations in automotive and aerospace manufacturing. Industrial pipes maintain precise measurements, providing stable and reliable fluid transport that is essential for precision machining processes.
7. Customization for Specific Applications
Automotive and aerospace manufacturing processes have diverse fluid transport requirements. Industrial pipes can be customized in terms of material composition, diameter, and length to suit the specific needs of different machining and assembly applications.
8. Joining Methods
Efficient joining methods, such as welding or specialized connectors, are crucial for industrial pipes in automotive and aerospace manufacturing. These methods ensure secure and leak-resistant connections, contributing to the overall safety and reliability of fluid transport systems.
9. Structural Support
Industrial pipes provide structural support for hydraulic systems used in automotive and aerospace manufacturing. They contribute to the stability and integrity of the overall manufacturing infrastructure, ensuring precise fluid transport and system reliability.
10. Durability Under External Forces
Industrial pipes are engineered to withstand external forces, vibrations, and dynamic conditions present in machining and manufacturing environments. This durability ensures the longevity and reliability of fluid transport systems.
11. Safety Compliance
Adherence to safety standards and regulations is paramount in manufacturing. Industrial pipes are manufactured to meet or exceed industry safety standards, providing a secure and reliable infrastructure for fluid transport in automotive and aerospace manufacturing.
12. Easy Maintenance and Inspection
Industrial pipes are designed for easy maintenance and inspection in automotive and aerospace manufacturing environments. Accessible areas for inspection facilitate regular checks, ensuring the ongoing reliability and safety of fluid transport systems.
In summary, industrial pipes are indispensable in the automotive and aerospace manufacturing industries, providing technical features that contribute to precise fluid transport, high-pressure handling, and overall system reliability. Their durability, precision, and adaptability make them critical components for ensuring the integrity and efficiency of manufacturing processes in these industries.
Discharge/Suction Hoses for Manufacturing
Anaconda Industrial Discharge & Suction Hoses play a pivotal role in the manufacturing and processing industries, offering technical advantages essential for material handling, fluid transfer, and maintaining operational efficiency. Here’s a technical description of the primary benefits of Anaconda Industrial Suction Hoses in manufacturing and processing applications:
1. Material Handling
Benefit: Efficient Handling of Raw Materials and By-Products
Suction hoses are designed for the efficient suction and transfer of raw materials, powders, and by-products in manufacturing processes.
Technical Advantage: Constructed with materials resistant to abrasion, the hoses ensure reliable and efficient material transfer while minimizing wear and tear.
2. Fluid Transfer
Benefit: Seamless Transfer of Liquids in Various Manufacturing Operations
Suction hoses facilitate the transfer of liquids such as chemicals, solvents, and process fluids in diverse manufacturing applications.
Technical Advantage: Engineered with materials compatible with different fluids, the hoses ensure reliable and efficient fluid transfer while maintaining integrity.
3. Flexibility and Maneuverability
Benefit: Adaptability to Complex Manufacturing Environments
Manufacturing facilities often feature intricate equipment setups and changing operational conditions. Suction hoses are designed with flexibility to navigate these environments.
Technical Advantage: The hoses’ flexibility ensures efficient and adaptable material transfer, suction, and discharge in diverse manufacturing scenarios.
4. Vacuum Resistance
Benefit: Optimized Suction Performance in Demanding Conditions
Suction hoses are engineered to withstand varying degrees of vacuum, ensuring effective suction of liquids and materials in different manufacturing applications.
Technical Advantage: The hoses’ vacuum resistance maintains structural integrity, optimizing suction performance and preventing collapse during demanding manufacturing processes.
5. Resistance to Abrasion
Benefit: Extended Service Life in Abrasive Manufacturing Environments
Manufacturing environments can be abrasive due to the presence of particles and debris. Suction hoses are constructed with materials offering high abrasion resistance.
Technical Advantage: This resistance ensures durability, reducing the need for frequent hose replacements and minimizing downtime in manufacturing operations.
6. Custom Sizing for Flow Optimization
Benefit: Tailored Solutions for Varied Manufacturing Flow Rates
Suction hoses are available in various sizes and diameters, allowing for customization based on the specific flow requirements of different manufacturing processes.
Technical Advantage: Proper sizing ensures optimal flow rates, minimizing energy consumption and pressure drops, and maximizing the efficiency of material transfer in manufacturing operations.
7. Chemical Resistance
Benefit: Compatibility with Chemicals in Specific Manufacturing Processes
Suction hoses can be manufactured with materials that offer resistance to chemicals encountered in manufacturing processes, such as cleaning agents and process chemicals.
Technical Advantage: Chemical resistance, when required, ensures that the hoses maintain structural integrity when exposed to potentially corrosive substances, contributing to a longer service life.
In summary, Anaconda Industrial Suction Hoses in the manufacturing and processing industries offer technical advantages, including efficient material handling, seamless fluid transfer, flexibility, vacuum resistance, resistance to abrasion, custom sizing, and optional chemical resistance. These features collectively contribute to the durability, adaptability, and overall effectiveness of suction hoses in meeting the unique challenges of manufacturing and processing applications.
Lay Flat Hose for Manufacturing
Industrial lay flat hoses are crucial in manufacturing and processing operations, providing technical advantages that optimize fluid transfer processes. Here’s a technical description of the key benefits of industrial lay flat hoses in manufacturing and processing industries:
1. Efficient Fluid Transfer
Benefit: Optimized Manufacturing Processes
Lay flat hoses enable efficient and precise fluid transfer, supporting manufacturing and processing operations. The flat design minimizes friction loss, ensuring fluids reach the desired areas with minimal energy loss, enhancing overall process efficiency.
2. Rapid Deployment and Retrieval
Benefit: Time-Saving Production Operations
The flat design allows for rapid deployment and retrieval, crucial for time-sensitive manufacturing processes. Quick hose handling enhances overall operational efficiency, reducing downtime and optimizing production timelines.
3. Compact Storage
Benefit: Space-Efficient Storage in Manufacturing Facilities
Lay flat hoses can be neatly rolled or folded into a compact form, minimizing space requirements in manufacturing facilities. This is advantageous for efficient logistics and inventory management within production environments.
4. Resistance to Chemicals
Benefit: Compatibility with Manufacturing Fluids
Industrial lay flat hoses are engineered with materials resistant to chemicals commonly found in manufacturing processes. This ensures compatibility with various fluids encountered in the industry, enhancing hose longevity and performance.
5. Flexibility and Maneuverability
Benefit: Adaptability to Dynamic Manufacturing Configurations
Lay flat hoses exhibit flexibility, allowing them to adapt to changing manufacturing configurations and contours. This flexibility ensures efficient material transfer and fluid handling in dynamic and challenging manufacturing environments.
6. High Burst Pressure Capability
Benefit: Reliability Under Pressure in Manufacturing Operations
Engineered with a high burst pressure capability, lay flat hoses maintain reliability even when subjected to elevated pressures during manufacturing processes. This ensures uninterrupted fluid transfer within production lines.
7. Uniform Fluid Distribution
Benefit: Consistent Transfer of Manufacturing Fluids
Lay flat hoses distribute fluids uniformly along their length, ensuring consistent transfer and distribution of liquids in manufacturing applications. This is critical for maintaining operational efficiency and optimizing fluid usage.
8. Compatibility with Manufacturing Equipment
Benefit: Seamless Integration with Production Machinery
Lay flat hoses are designed for compatibility with manufacturing pumps and equipment. The fittings and couplings ensure a secure connection, minimizing the risk of leaks and optimizing fluid transfer efficiency within manufacturing systems.
9. Custom Sizing for Flow Optimization
Benefit: Tailored Solutions for Varied Manufacturing Flow Rates
Lay flat hoses are available in various sizes and diameters, allowing for customization based on the specific flow requirements of different manufacturing applications. This ensures optimal fluid transfer rates and minimizes energy consumption.
10. Temperature Resistance
Benefit: Suitability for Varied Manufacturing Climates
Engineered to withstand a broad temperature range, these hoses remain functional in diverse manufacturing climates. Their flexibility and reliability are maintained even in extreme temperature conditions encountered in industrial production settings.
In summary, industrial lay flat hoses offer technical benefits that contribute to the efficiency, durability, and adaptability of fluid transfer processes in manufacturing and processing industries. Their chemical resistance, high burst pressure capability, and compatibility with production equipment make them essential components for optimizing manufacturing operations.